Coincidentally, have you ever wondered how long ceramic coatings can last? The longevity of these coatings is a topic that sparks curiosity among many vehicle owners. Understanding the factors that influence their durability is key to making informed decisions when it comes to protecting your vehicle’s surface. By uncovering the secrets behind their lifespan, you’ll be equipped with valuable knowledge to help you maximize your ceramic coating investment.
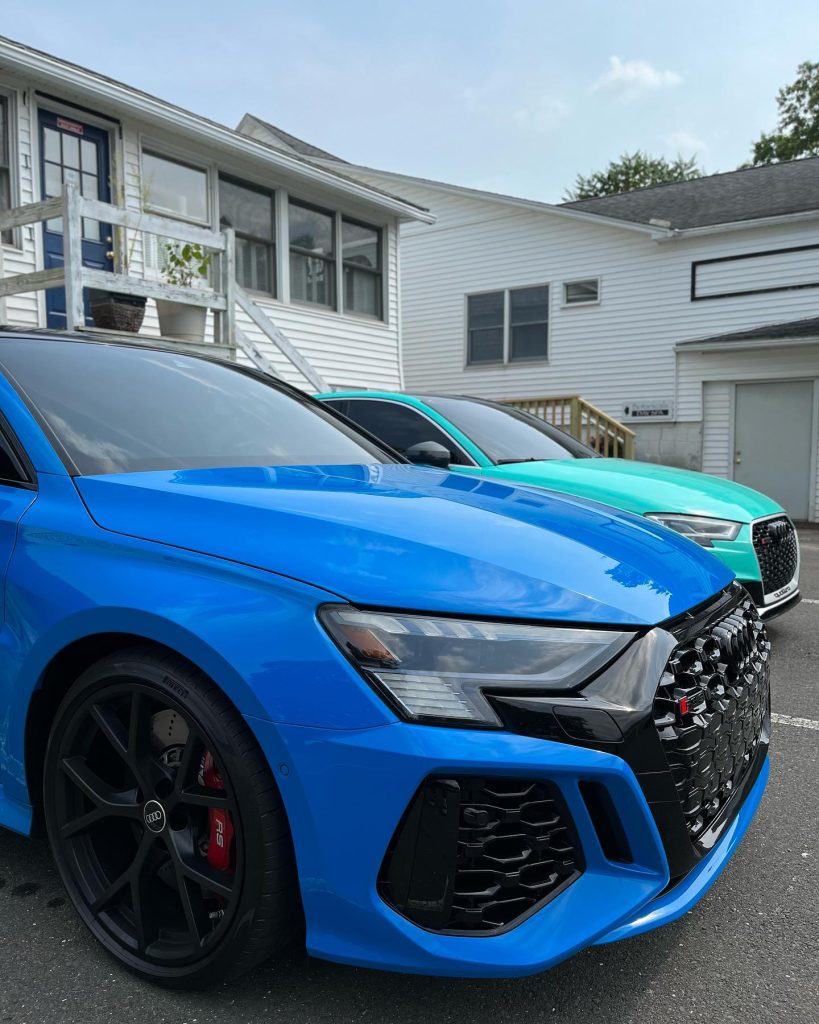
Key Takeaways
- Ceramic coatings typically last between 2 to 5 years.
- Factors include maintenance practices and environmental conditions.
- Proper application techniques and maintenance routines extend longevity.
- Quality of initial application and surface type influence durability.
- Understanding material composition and maintenance is crucial for lifespan.
Types of Ceramic Coatings
Ceramic coatings are classified into several types based on their composition and properties. Understanding these types is essential for making informed decisions regarding the durability of ceramic coatings.
The application methods, benefits, cost, and effectiveness of ceramic coatings vary depending on the type chosen.
One common type of ceramic coating is silicon dioxide-based coatings (SiO2). These coatings are known for their excellent hydrophobic properties, making them effective at repelling water and contaminants. They’re typically applied using spray or wipe-on methods, providing a relatively easy application process. The benefits of silicon dioxide coatings include enhanced shine and protection against UV rays, water spots, and chemical etching. While these coatings are generally cost-effective, their durability may vary based on the quality of the product and the application process.
Another type of ceramic coating is titanium dioxide-based coatings (TiO2). These coatings offer exceptional durability and resistance to scratches and chemicals. They’re often applied using professional methods such as machine buffing to guarantee uniform coverage. The benefits of titanium dioxide coatings include long-lasting protection and a high level of gloss. Although ceramic coatings are primarily composed of 15-20% SiO2 and TiO2, with SiO2 being the main ingredient
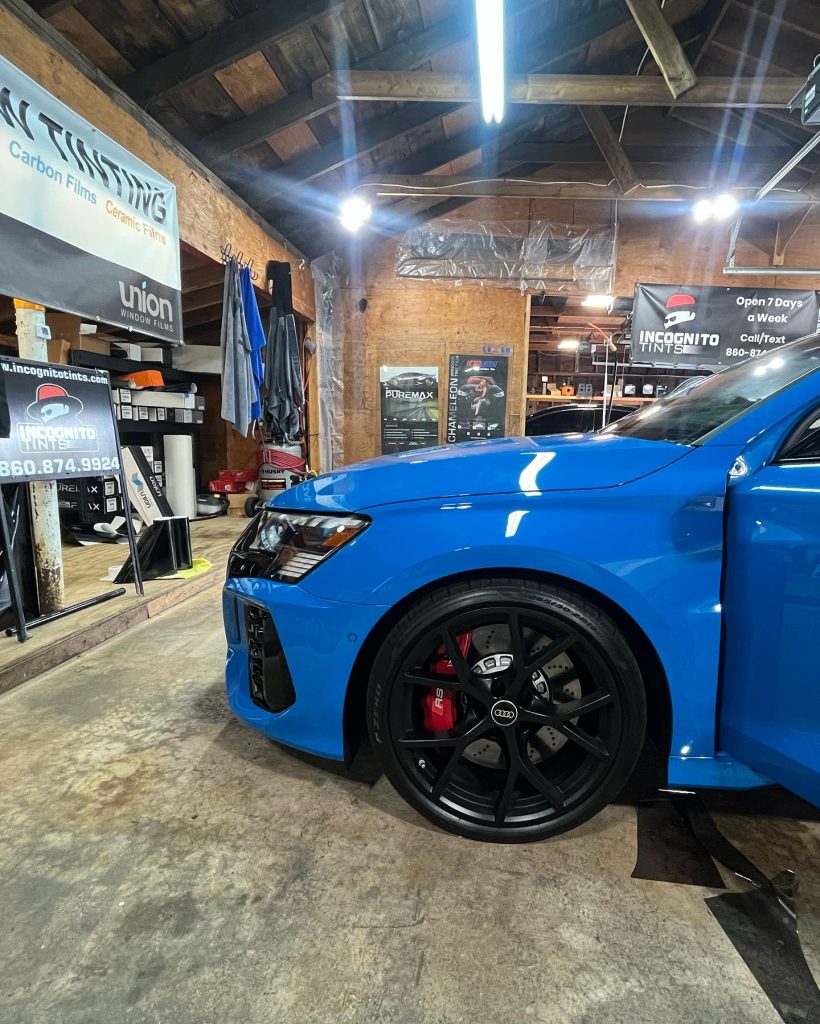
Factors Affecting Longevity
To enhance the longevity of ceramic coatings, you must consider the impact of material composition. Understanding how the composition of the coating interacts with external elements is essential for durability.
Guarantee proper application techniques. Adopting precise application methods and monitoring exposure levels will be key factors in prolonging the lifespan of ceramic coatings.
Evaluate the effects of environmental exposure. This involves assessing how environmental factors such as UV radiation, moisture, and temperature fluctuations affect the coating over time.
Material Composition Impact
The composition of ceramic coatings greatly influences their durability and lifespan. When considering the impact of material composition, two essential factors to evaluate are chemical resistance and heat retention.’
Ceramic coatings with high chemical resistance are more durable as they can withstand exposure to harsh chemicals without degrading. This property is critical for applications where the coating is exposed to corrosive substances or environments.
Additionally, heat retention plays a significant role in determining the longevity of ceramic coatings. Coatings that have excellent heat retention properties are better able to withstand high temperatures without deteriorating, making them suitable for applications where heat resistance is essential.
Proper Application Techniques
Properly applying ceramic coatings is vital for maximizing their longevity and durability in various applications. Application mistakes can greatly impact the effectiveness of the coating, leading to premature wear and reduced protection.
One of the common misconceptions is that more layers of ceramic coating will automatically provide better durability. However, applying too many layers can lead to uneven thickness and curing issues, compromising the overall performance.
To ensure ideal longevity, it’s important to follow the manufacturer’s guidelines regarding application techniques, including surface preparation, curing times, and proper application tools. Neglecting these recommendations can result in poor adhesion, bubbling, or peeling of the coating over time.
Additionally, applying ceramic coatings in extreme temperatures or high humidity levels can also affect the curing process and overall durability.
Environmental Exposure Effects
Appropriate environmental conditions play an important role in determining the longevity and performance of ceramic coatings. Factors such as UV exposure, humidity impact, temperature changes, and pollution effects greatly influence the durability of these coatings.
UV exposure can cause degradation of the coating’s chemical structure, leading to discoloration and reduced protective properties. Humidity impact, especially in high-moisture environments, can promote corrosion and delamination of the ceramic coating.
Temperature changes can result in thermal expansion and contraction, potentially causing cracking or peeling of the coating. Pollution effects, including exposure to chemicals and contaminants in the air, can accelerate the deterioration of ceramic coatings over time.
Understanding how these environmental factors interact with ceramic coatings is important for predicting their longevity and performance. By considering these influences, proper maintenance schedules and protective measures can be implemented to ensure the durability of ceramic coatings in various environmental conditions.
Proper Application Techniques
When applying ceramic coatings, make sure that the method used aligns with manufacturer guidelines for best performance and longevity. Proper surface preparation is essential before applying the ceramic coating to guarantee ideal adhesion. This involves thorough cleaning to remove any dirt, grease, or residue that could impede the bonding process. Additionally, checking the curing process is fundamental as it directly impacts the coating’s durability. Following the curing guidelines specified by the manufacturer will help achieve the desired protective properties.
Maintaining the correct application thickness is crucial for the ceramic coating to provide maximum protection. Applying the coating too thinly may result in inadequate coverage, reducing its effectiveness, while applying it too thickly can lead to longer drying times and potential issues with curing. It’s advisable to follow the manufacturer’s instructions regarding the application thickness to ensure ideal performance.
Drying time is another vital factor to consider during the application process. Allowing the ceramic coating to dry for the recommended period is necessary to ensure it cures properly and forms a durable protective layer. Rushing the drying process can compromise the coating’s integrity and longevity. By adhering to the specified drying time, you can enhance the durability of the ceramic coating and maximize its protective properties.
Maintenance Tips for Longevity
To safeguard the extended longevity of ceramic coatings, diligent maintenance practices are vital for preserving their protective properties over time. Cleaning techniques play a critical role in maintaining the effectiveness of ceramic coatings. Regularly washing the coated surface with a pH-neutral car shampoo and a soft microfiber wash mitt helps remove dirt, grime, and other contaminants that can compromise the coating’s performance. Avoid using harsh chemicals or abrasive tools during cleaning to prevent scratching or damaging the coating.
In addition to proper cleaning techniques, implementing protective measures can further enhance the durability of ceramic coatings. Applying a ceramic coating booster or spray sealant every few months can help rejuvenate the coating’s hydrophobic properties and reinforce its protective layer. Using a ceramic coating-specific maintenance spray can also help maintain the coating’s gloss and water-beading capabilities between regular washes.
Furthermore, avoiding exposure to harsh environmental elements, such as direct sunlight, bird droppings, and tree sap, can prolong the lifespan of ceramic coatings. Parking in shaded areas or using a car cover can provide an extra layer of protection against UV rays and potential contaminants.
Realistic Lifespan Expectations
When considering the realistic lifespan expectations of ceramic coatings, it’s essential to understand the expected lifespan ranges. The various factors that can affect durability are also crucial to consider
.
Additionally, the maintenance practices necessary for prolonging the coating’s life play a significant role. By analyzing these key points, you can better assess the longevity of ceramic coatings in different environments and under varying conditions, enabling you to make informed decisions regarding their application and upkeep.
Understanding the interplay of expected lifespan, influencing factors, and maintenance requirements is vital for optimizing the performance and durability of ceramic coatings in practical use scenarios.
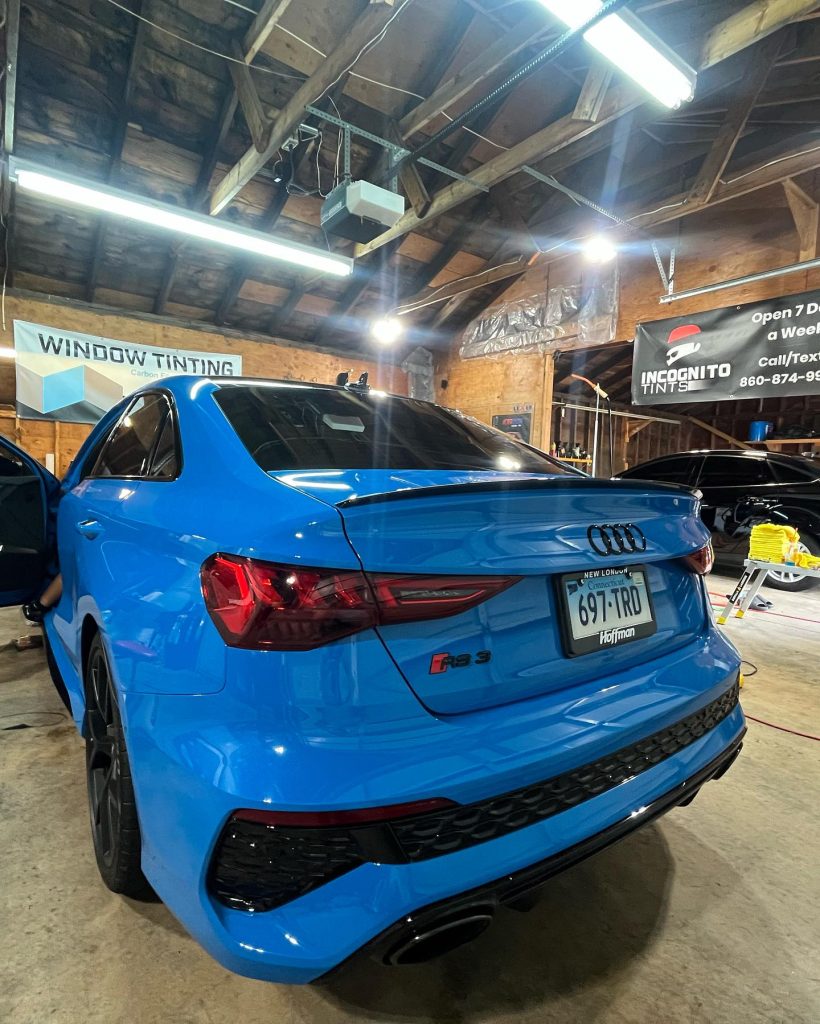
Expected Lifespan Ranges
Achieving a realistic understanding of the expected lifespan ranges of ceramic coatings is important for informed decision-making in various industries. When considering longevity expectations, it’s vital to acknowledge that the lifespan of ceramic coatings can vary significantly based on maintenance practices and environmental conditions. Typically, ceramic coatings are designed to last between two to five years, depending on these factors.
Factors that influence the durability of ceramic coatings include:
- The quality of the initial application
- The type of surface it’s applied to
- The level of exposure to harsh environmental conditions like UV radiation, humidity, and temperature fluctuations
Proper maintenance practices, such as regular cleaning and inspection for damage, can help extend the lifespan of ceramic coatings.
Understanding the expected lifespan ranges of ceramic coatings allows industries to:
- Plan for maintenance schedules effectively
- Budget for reapplications when necessary
- Maintain the optimal performance of these coatings over time
Factors Affecting Durability
Understanding the factors that influence the durability of ceramic coatings is essential for establishing realistic lifespan expectations in various industries. The maintenance frequency plays a pivotal role in prolonging the lifespan of ceramic coatings. Regular upkeep, such as cleaning and inspections, can prevent premature wear and tear, ensuring the coating remains intact for an extended period.
Environmental conditions also greatly impact durability. Harsh climates, exposure to UV radiation, and chemical contaminants can degrade the coating faster, reducing its lifespan.
Moreover, the quality of the application is a key factor in determining how long a ceramic coating will last. Proper application techniques, including surface preparation and curing processes, are vital for maximizing durability. A well-applied coating is more resistant to wear and tear, enhancing its longevity.
Wear and tear, inevitable in most industries, can gradually degrade the coating over time. By understanding these factors and taking proactive measures to address them, you can set realistic expectations for the durability of ceramic coatings in your specific applications.
Maintenance for Longevity
Maintenance practices significantly influence the realistic lifespan expectations of ceramic coatings in various industries. Proper cleaning techniques are vital to preserve the integrity of the coating. Regular maintenance routines, such as gentle washing with suitable cleaning agents and avoiding abrasive materials, help to prevent premature wear and maintain the coating’s protective properties.
Protective measures, like applying additional layers of ceramic coating or using sealants, can further extend the longevity of the coating.
Implementing a structured maintenance schedule customized to the specific coating type and environmental conditions is essential for maximizing durability. Monitoring the coating for any signs of deterioration and addressing them promptly can prevent extensive damage and prolong its lifespan.
Comparing Durability Across Brands
When evaluating ceramic coatings, it’s vital to compare the durability levels offered by different brands to make an informed decision on the most suitable option for your needs.
Brand comparison and longevity testing play a pivotal role in determining the longevity of ceramic coatings.
Here is a breakdown of key factors to keep in mind when comparing durability across brands:
- Product Composition: Different brands may use varying formulations and technologies in their ceramic coatings, impacting their durability. Analyzing the composition can give you insights into how long the coating is likely to last.
- Testing Standards: Look for brands that conduct thorough durability analysis. Brands that adhere to industry standards and perform extensive testing can provide more reliable information on the lifespan of their coatings.
- Customer Feedback: While not as quantitative as lab testing, customer reviews and feedback can offer valuable insights into the real-world performance of ceramic coatings from different brands. Taking into account the experiences of other users can help you gauge the durability of a particular brand’s product.
Extending the Lifespan of Coatings
To enhance the duration of ceramic coatings, implementing proper application techniques is essential for maximizing their durability and performance. Protective measures play a pivotal role in ensuring the extended lifespan of these coatings.
When applying ceramic coatings, it’s imperative to follow manufacturer guidelines meticulously. This includes surface preparation, cleaning, and ensuring the correct curing time for best adhesion.
Longevity enhancements can also be achieved by incorporating additional protective layers or top coatings. These extra layers act as barriers against environmental factors such as UV radiation, chemicals, and physical abrasions, further safeguarding the ceramic coating underneath.
Regular maintenance, through gentle cleaning methods and periodic inspections, can help identify any areas that may require touch-ups or reapplications.
Furthermore, utilizing ceramic coatings that have been specifically formulated for longevity can profoundly impact the overall lifespan of the coating. These formulations often contain advanced chemical compositions that enhance resistance to wear and tear, thereby extending the protective capabilities of the coating.
The durability of ceramic coatings can vary based on multiple factors, including material composition, application methods, and maintenance practices. By understanding these variables and following the recommended guidelines, you can maximize the lifespan of your ceramic coating.
While the standard lifespan of 2 to 5 years is common, some high-quality coatings have been known to last even longer, showcasing the potential for extended protection. Further research and advancements in ceramic coating technology may continue to push future durability boundaries.